Increasing the efficiency of mechanical ventilators during pandemics through additive manufacturing
DOI:
https://doi.org/10.17305/bjbms.2020.5165Keywords:
COVID-19, multiplexer, additive manufacturingAbstract
The COVID-19 pandemic tested medical facilities’ readiness in terms of the number of available mechanical ventilators. Most countries raced to stock up on ventilators, which created a surge in demand and short in supply. Furthermore, other means of coping with the demand were proposed, such as using additive manufacturing. The purpose of this paper was to test whether the addition of 3D-printed splitters would help deliver required tidal volume to each patient, while supporting four patients on a single ventilator for 24 hours on pressure mode at 25-cm H2O, and to determine whether a fifth patient can be ventilated. The ventilation of four human lungs was simulated using 3D printed parts, a single ventilator, four test-lungs, and standard tubing. Peak pressure, positive end-expiratory pressure, total tidal volume, individual tidal volume, total minute volume, and individual tidal volume data were collected. Usage of a 3D printed small size splitter enabled a 26% increase in individual tidal volume compared to standard tubing and a series of two-way splitters. The ventilator was able to supply the required pressure and tidal volume for 24 hours. A single ventilator with a four-way splitter can ventilate four patients experiencing respiratory failure for at least 24 hours without interruption. The equipment cannot sustain ventilating a fifth patient owing to minute volume limitation. This study expands on an earlier study that tested similar circuitry and reveals that the desired individual tidal volume is achieved. However, further research is required to provide the monitoring ability of individual patient parameters and prevention of cross-contamination.
Citations
Downloads
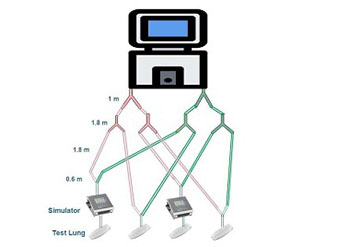
Downloads
Additional Files
Published
Issue
Section
Categories
How to Cite
Accepted 2020-09-26
Published 2021-04-01